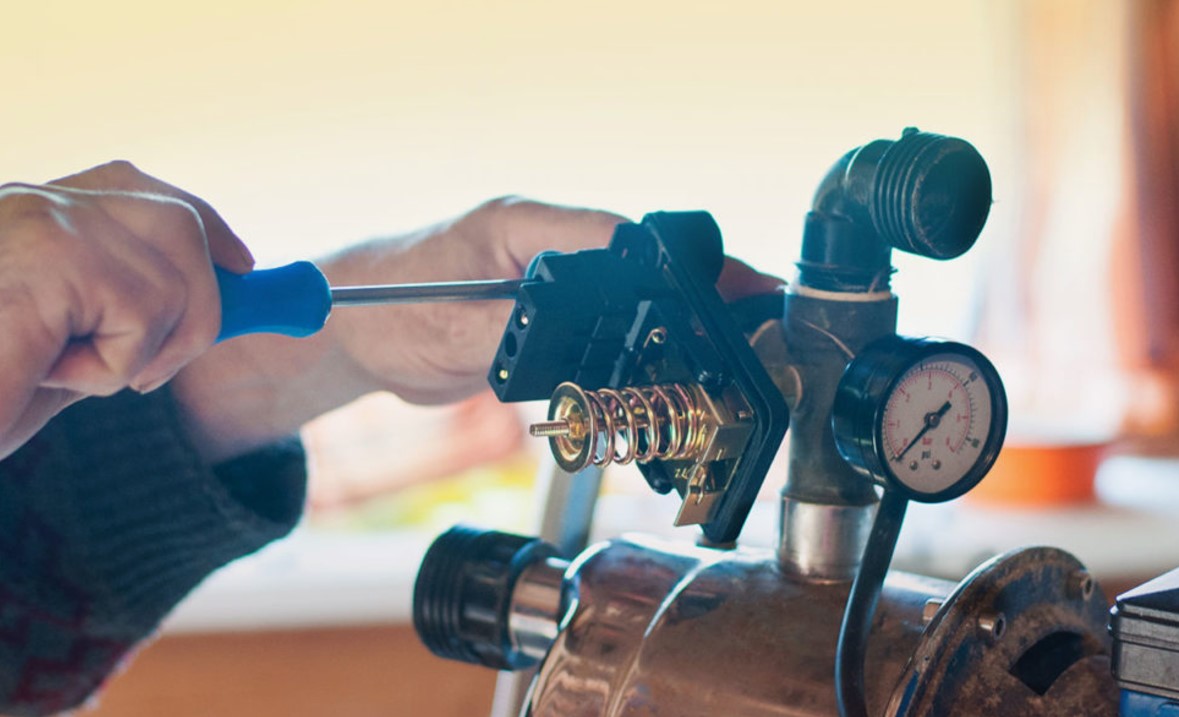
Industrial pumps are essential in many different industries, such as mining, manufacturing, water treatment, and oil and gas. Transporting commodities like chemicals, water, slurries, and other substances is crucial for a variety of industrial applications. Like any other frequently used equipment, industrial pumps are prone to wear and tear over time. This emphasizes how crucial repair and pump overhaul services are to maintaining continuous operational efficacy, safety, and affordability.
In this blog, we shall explore the subtleties of pump repair and overhaul services. We’ll review the steps needed in an overhaul, how preventive maintenance can maximize pump performance, and the warning signals that a pump might need repair.
Why Industrial Pumps Need Repair and Overhaul
Industrial pumps work in harsh conditions and frequently handle caustic or abrasive materials at high pressure. This extensive use erodes vital components over time, compromising dependability and efficiency. A worn-out or subpar pump can result in reduced flow rates, higher energy consumption, and even catastrophic failure.
Think about the financial consequences of a single pump failure to appreciate the need for prompt pump repairs. Studies have shown that unplanned downtime expenses in some industries can average $260,000 per hour, and in facilities that largely rely on pumps, they can account for as much as 30% of equipment downtime. A pump overhaul can increase the pump’s lifespan and avoid these costly concerns.
Knowing When to Repair a Pump
Proactive maintenance starts with knowing when your pump needs maintenance. These are a few important indicators:
Decreased Performance: If the pump’s flow rates, pressure drops, or irregular functioning decrease, it obviously has trouble and probably needs to be repaired.
Increased Vibrations or Noise: Pumps ought to run smoothly. Unusual vibrations or excessive noise may indicate mechanical problems such as cavitation, imbalanced rotors, or worn bearings or impellers.
Growing Energy Use: An ineffective pump uses more energy. An abrupt increase in energy expenses without a commensurate rise in effort may indicate wear in the pump’s constituent parts.
Leaking Seals or Valves: Seals and valves keep the pump system airtight. Leaks are a clear sign of deteriorating components that require immediate attention to avoid contamination or loss of valuable products.
Excessive Heat: Pumps naturally generate heat, but when bearings or other components wear out, they may produce excessive heat, which is inefficient and damaging over time.
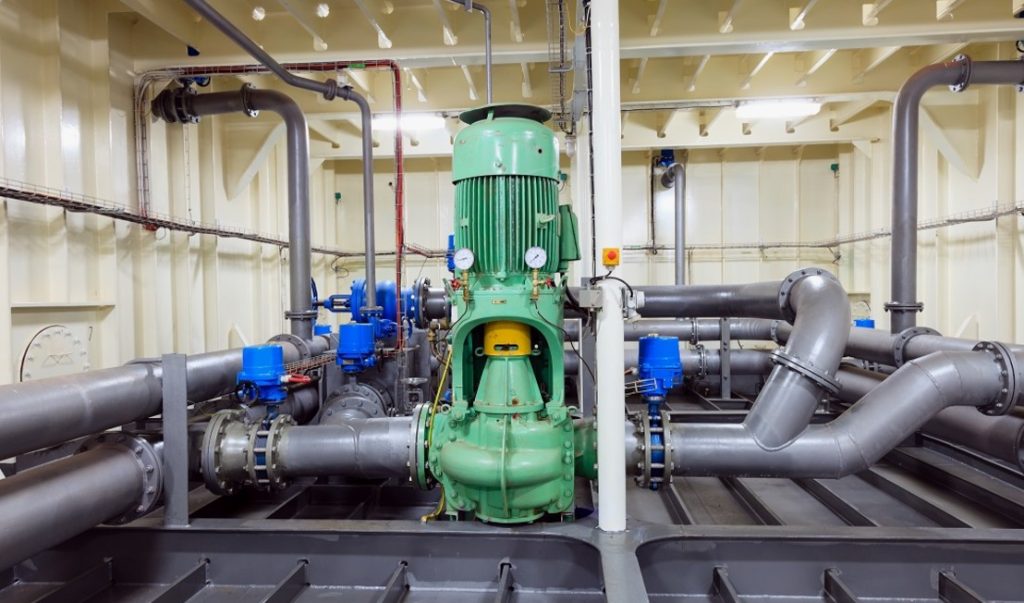
The Process of Pump Overhaul: What’s Involved?
A pump overhaul is a comprehensive inspection, repair, and reconditioning process designed to restore the pump to optimal performance. Here’s an overview of the main steps involved:
Disassembly and Cleaning: The pump is carefully disassembled to inspect each component. Parts are thoroughly cleaned to remove any buildup or contaminants that may have contributed to wear.
Component Inspection: Every part, including seals, bearings, impellers, and shafts, is inspected for signs of wear. Advanced diagnostics, such as non-destructive testing (NDT), can reveal microscopic cracks or weaknesses that might compromise pump reliability.
Replacement of Worn Parts: Damaged or worn-out parts are replaced with new or reconditioned components. High-quality materials ensure durability, particularly if the pump handles abrasive or corrosive materials.
Reassembly and Balancing: The pump is meticulously reassembled. Technicians use balancing tools to ensure that rotating parts are balanced and aligned for smooth operation, reducing vibration and extending the lifespan of bearings and seals.
Testing and Calibration: After reassembly, the pump undergoes rigorous testing to verify that it meets or exceeds operational standards. This phase ensures reliability and efficiency before returning the pump to service.
The Financial and Operational Benefits of a Pump Overhaul
Beyond mitigating downtime, pump overhaul services offer significant financial benefits. Studies reveal that a well-maintained pump can improve energy efficiency by up to 15-25%. The potential savings are substantial since they account for 10% of global electricity consumption, especially in industries where pumps run continuously.
Moreover, proactive maintenance and overhauls reduce the likelihood of emergency repairs, costing up to four times more than planned maintenance. For a company operating dozens or even hundreds of pumps, these savings can have a powerful impact on the bottom line.
Preventive Maintenance: The Key to Avoiding Costly Overhauls
While overhauls are essential for pumps that have seen extended service, implementing preventive maintenance practices can further reduce downtime and repair costs. Routine inspections, alignment checks, lubrication, and eyeing for any early wear or strain are all components of preventive maintenance. Maintenance crews can identify possible issues before they become more serious by monitoring performance indicators like vibration, temperature, and energy usage.
Technological advancements also support preventive maintenance. For instance, predictive maintenance systems that use IoT sensors can monitor pumps in real-time, alerting operators to changes in operational parameters. This allows maintenance to be scheduled only when necessary, optimizing time and resources.
Case Study: The Value of a Pump Overhaul in Action
One notable example of pump overhaul benefits comes from a water treatment facility that relied on centrifugal pumps to treat and distribute water to a large city. After noticing a gradual decrease in flow rate and efficiency, the facility overhauled its primary pumps. Technicians replaced worn impellers, realigned rotors, and upgraded seals and bearings. Post-overhaul, the pumps delivered a 20% improvement in efficiency, significantly reducing energy costs and a prolonged operational lifespan. The facility saved an estimated $300,000 annually due to these efficiency gains and reduced emergency repairs.
Key Takeaway: Trial pump repair and overhaul services
These are pivotal in maintaining operational efficiency, reducing downtime, and controlling costs. By addressing wear and tear proactively and engaging in regular preventive maintenance, facilities can extend the lifespan of their pumps, achieve substantial energy savings, and minimize the risk of unexpected breakdowns. As the demands on industrial pumps continue to grow, understanding and investing in overhaul services has never been more crucial.
For companies that rely heavily on pumps, adopting a holistic approach to maintenance can ensure that pumps remain a valuable, cost-effective part of their operations. By recognizing the signs of wear, investing in high-quality overhauls, and embracing preventive maintenance, businesses can ensure they’re always operating at peak performance—today and in the future.
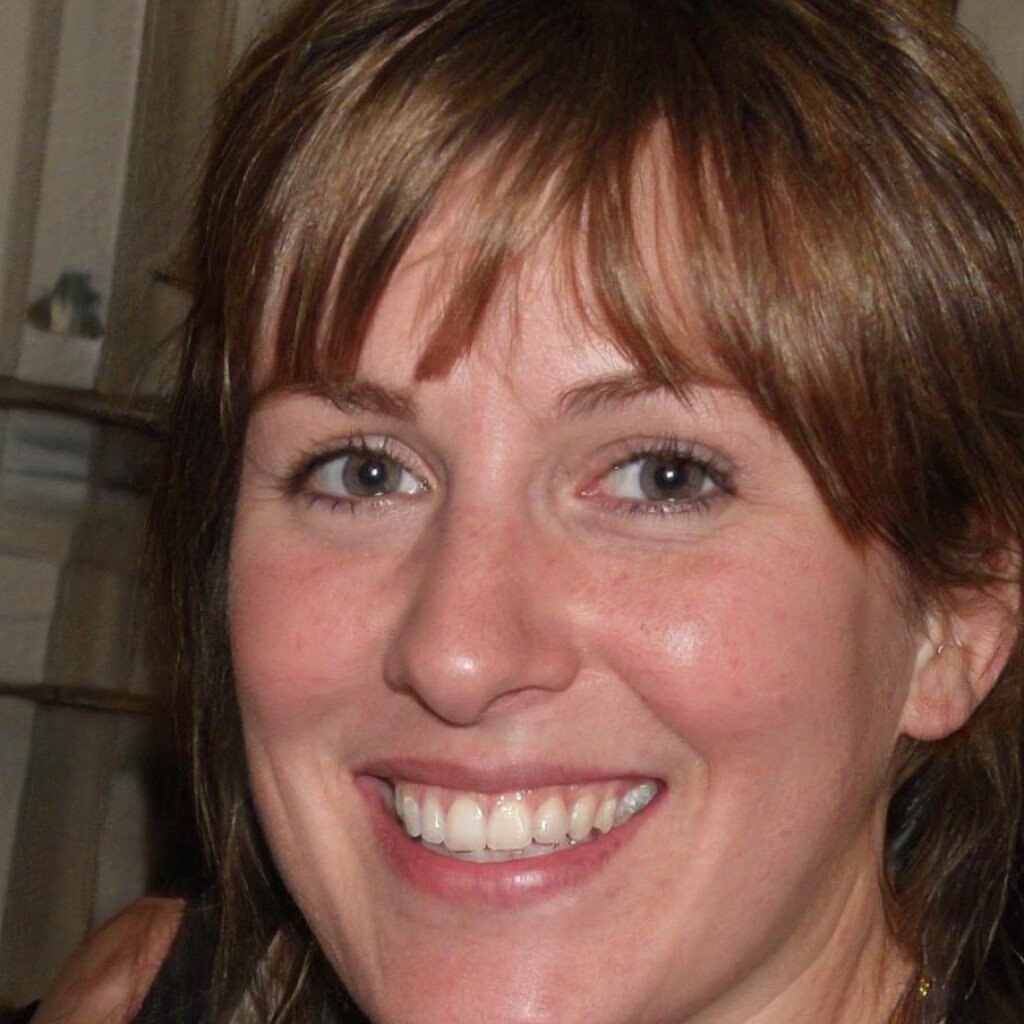
Soccer lover, nature enthusiast, guitarist, Bauhaus fan and critical graphic designer. Doing at the fulcrum of minimalism and purpose to craft experiences that go beyond design. I am 25 years old.